Dive into the World of Warehousing and Racking
4 Questions To Get Your Rack Solution
The dimensions of your facility play a crucial role in designing an effective storage rack system.
For facilities with lower ceiling heights (20 feet or less), selective racking may be the best choice. On the other hand, warehouses with 40-foot-high ceilings can accommodate automated storage and retrieval systems (AS/RS) served by stacker cranes.
In smaller warehouses, achieving high-density storage might be a priority. Various rack systems are designed to maximize unit load density while sacrificing direct access to goods. These include:
The characteristics of your inventory are crucial in determining the most suitable storage rack type. Factors such as unit load dimensions, weight, and uniformity are essential considerations.
Depending on the load type, options like long-span shelving, carton flow rack systems, or adjustable pallet racking systems may be recommended.
Inventory turnover rates vary among different products, which can influence the choice of industrial racking systems. Products with fast turnover requirements, such as perishable goods or fashion accessories, need quick access to minimize spoilage or obsolescence.
For fast stock rotation, systems like FIFO pallet racks, Pallet Flow racks, Drive-Through racks, or Pallet Shuttle racks are ideal choices. These systems ensure that the first product in is also the first one out.
Some products require specific environmental conditions to prevent deterioration, such as refrigerated or freezer space for food, beverage, or pharmaceutical products. It's essential to address rack specification questions related to handling requirements.
In cold storage or freezer zones, storage systems supporting uniform temperatures and cold air circulation are common. Mobile racking, Drive-In systems, and Pallet Shuttle racks are often deployed in these environments.
For facilities storing hazardous products like chemicals, it's crucial to inform the rack manufacturer about the chemical compounds to ensure compatibility and reduce the risk of corrosion or rust affecting the rack.
Getting Started
Introduction
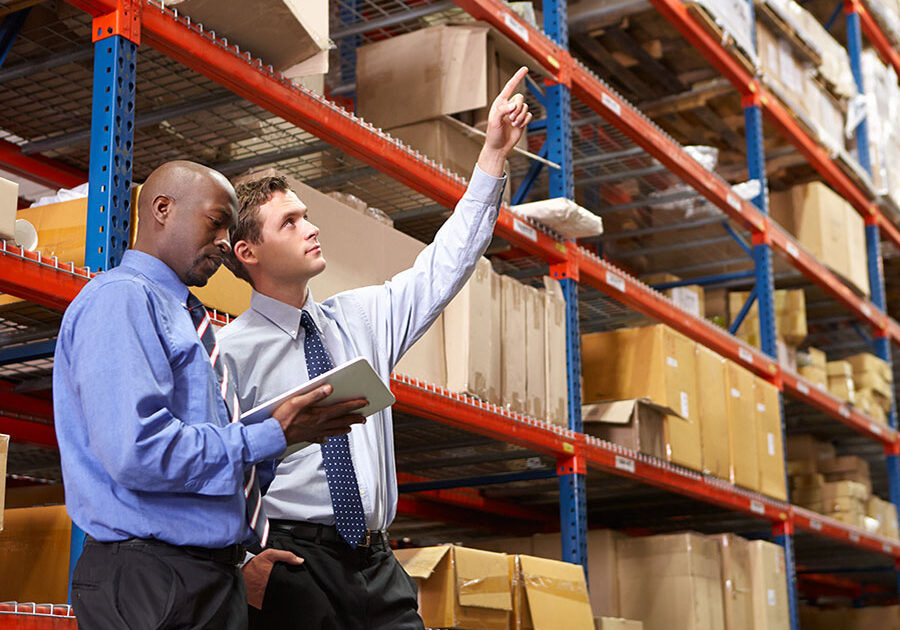
Welcome to our comprehensive guide on pallet racking systems in the warehouse industry. If you’re looking to optimize your warehouse for efficiency and safety, you’ve come to the right place.
The More You Know!
Types of Pallet Racking
When it comes to pallet racking in the warehouse industry, there are several types to consider:
Selective Pallet Racking: Flexible and Accessible Storage Solutions
Selective pallet racking is the most common type of racking system, designed to offer direct access to each pallet, making it ideal for facilities that require high selectivity. This versatile system maximizes storage space while maintaining easy access to individual pallets, making it a great choice for warehouses with a wide variety of products.
Key Benefits of Selective Pallet Racking:
- Direct Access: Each pallet is accessible without having to move others, simplifying inventory management and reducing handling time for your team.
- Cost-Effective: Selective racking is one of the most affordable racking systems to install and maintain, making it a budget-friendly option for warehouses of all sizes.
- Flexible Design: It can be easily adapted to fit different pallet sizes and configurations, ensuring that your storage layout is optimized for your specific needs.
- Easy Integration: Compatible with most types of forklifts, this system allows for smooth and efficient material handling operations.
- Scalable: As your business grows, selective racking can be easily expanded to accommodate increased inventory without requiring a complete overhaul of your storage system.
Is Selective Pallet Racking Right for You?
Selective pallet racking is the perfect solution for warehouses that prioritize product accessibility and require a high level of SKU variety. It is ideal for industries like logistics, manufacturing, and distribution centers where inventory turnover and order accuracy are crucial.
For more information on how selective pallet racking can enhance your warehouse's efficiency and organization, contact us today to find a solution tailored to your needs.
Drive-In / Drive-Thru Racking: High-Density Storage for Maximum Space Efficiency
Drive-In and Drive-Thru racking systems are designed to maximize storage density by allowing forklifts to drive directly into the rack's structure. These systems utilize a last-in, first-out (LIFO) or first-in, first-out (FIFO) approach, depending on the specific setup. Drive-In/Drive-Thru racking is ideal for operations with large quantities of similar products and limited SKU diversity.
Key Benefits of Drive-In / Drive-Thru Racking:
- Maximum Storage Density: These systems can increase your warehouse’s storage capacity by up to 75%, making them one of the most space-efficient racking options available.
- Cost-Effective Space Utilization: By eliminating aisles between racks, Drive-In/Drive-Thru systems allow you to store more pallets in the same square footage, reducing the need for additional storage space.
- Ideal for Bulk Storage: Best suited for high-volume inventory with low SKU variety, this system efficiently handles large quantities of similar items.
- Flexibility: Drive-In systems operate on a LIFO basis, while Drive-Thru systems can be configured for FIFO operations, providing flexibility depending on your inventory needs.
- Durable and Robust: Built to handle the rigors of high-density storage, these systems are designed to withstand the frequent loading and unloading of pallets.
Is Drive-In / Drive-Thru Racking Right for You?
Drive-In and Drive-Thru racking are perfect for industries with seasonal products or items that require cold storage, such as food and beverage, chemicals, and other bulk storage environments. If your warehouse prioritizes storage density and can operate on a LIFO or FIFO basis, this system may be an excellent fit.
For more information on how Drive-In / Drive-Thru racking can optimize your warehouse storage, contact us today for a customized solution tailored to your needs.
Cantilever Racking: The Ultimate Solution for Long and Bulky Items
Cantilever racking systems are specifically designed to store long, bulky, or irregularly shaped items that cannot be easily stored on traditional pallet racks. This system features horizontal arms that extend from a central column, providing unobstructed storage space ideal for items like lumber, pipes, steel bars, and furniture. Cantilever racking maximizes both vertical and horizontal storage space while ensuring easy access to every item.
Key Benefits of Cantilever Racking:
- Versatile Storage: Perfect for storing a wide range of products, including long, oversized, or awkwardly shaped items that don’t fit on standard pallet racking.
- Easy Accessibility: Open-front design allows for quick loading and unloading from the front without any vertical obstructions, making it simple to handle materials with forklifts or manually.
- Scalable Design: Cantilever racking can be easily expanded or reconfigured to accommodate changing inventory needs, providing flexibility as your business grows.
- Durable Construction: Built to handle heavy loads, cantilever systems are constructed from robust materials designed to withstand the demands of industrial environments.
- Optimized Space Utilization: This racking system efficiently utilizes vertical space, making it ideal for maximizing storage capacity in your warehouse or yard.
Is Cantilever Racking Right for You?
Cantilever racking is an ideal solution for industries like construction, manufacturing, and home improvement, where storing long and bulky items efficiently is crucial. It's perfect for businesses that need a flexible and durable storage system to manage their unique inventory.
For more information on how cantilever racking can enhance your storage capabilities, contact us today to design a solution that fits your specific requirements.
A Very Narrow Aisle (VNA) pallet racking system is designed to maximize warehouse space by significantly reducing aisle width between racks. This system is ideal for warehouses looking to improve storage density without expanding the facility’s footprint. By optimizing aisle width, VNA racks allow for more pallets to be stored while still maintaining accessibility for specialized forklifts.
Key Benefits of VNA Pallet Racking:
• Increased Storage Density: VNA systems can boost your warehouse’s storage capacity by up to 40%, making them perfect for high-volume storage environments.
• Efficient Space Utilization: By reducing aisle width, more of your warehouse’s floor space is dedicated to storage, rather than being taken up by wide aisles.
• Accessibility: Though the aisles are narrower, VNA systems are still fully accessible via specialized narrow-aisle forklifts or turret trucks, ensuring that goods can be easily retrieved without disruption.
• Improved Productivity: The streamlined layout can reduce travel time for forklifts, improving overall warehouse efficiency.
• Compatibility: VNA racking is compatible with most warehouse automation systems, making it future-proof for businesses looking to scale.
Is VNA Racking Right for You?
VNA pallet racking is particularly well-suited for operations with high SKU counts and limited warehouse space, where optimizing vertical and horizontal storage space is crucial. It is also ideal for industries like e-commerce, automotive parts, and food and beverage storage, where efficient space use is key.
For more information on how VNA pallet racking can transform your warehouse storage, contact us today for a customized solution that fits your needs.
Push-Back Racking Systems: Efficient Storage with Easy Access
A Push-Back racking system is designed to maximize your warehouse's storage efficiency by utilizing a last-in, first-out (LIFO) system. Unlike traditional racking, Push-Back systems allow multiple pallets to be stored on inclined rails, where they can be easily accessed and retrieved. This setup is ideal for warehouses looking to optimize space and streamline their inventory management.
Key Benefits of Push-Back Racking:
- Increased Storage Density: Push-Back racking can increase storage capacity by up to 75% compared to standard racking systems, making it perfect for facilities that need to store a large number of SKUs.
- Efficient Space Utilization: By allowing multiple pallets to be stored in a single lane, this system makes the most of both vertical and horizontal warehouse space.
- Easy Accessibility: Pallets are loaded and unloaded from the same aisle, which reduces the need for multiple access points and simplifies inventory retrieval.
- Improved Productivity: Push-Back systems reduce forklift travel time by consolidating storage areas, allowing for quicker and more efficient loading and unloading operations.
- Versatility: Compatible with a wide range of pallet sizes, this system is ideal for various industries including retail, manufacturing, and distribution centers.
Is Push-Back Racking Right for You?
Push-Back racking is best suited for operations with high inventory turnover and limited warehouse space, where optimizing both storage density and picking efficiency is essential. It's particularly useful in industries like food and beverage, retail, and consumer goods, where product accessibility and quick stock rotation are critical.
For more information on how Push-Back racking can enhance your warehouse's storage capabilities, contact us today for a customized solution that meets your needs.
Pallet Flow / Carton Flow Racking: Gravity-Driven Efficiency for High-Density Storage
Pallet flow and carton flow racking systems use gravity to streamline inventory rotation and improve order-picking efficiency. These dynamic storage systems are designed for first-in, first-out (FIFO) inventory management, ideal for warehouses that require high throughput and quick access to stock. Pallet flow racks move pallets smoothly on roller tracks, while carton flow racks utilize inclined shelves for smaller items, making them perfect for fast-paced picking environments.
Key Benefits of Pallet Flow / Carton Flow Racking:
- Increased Storage Density: These systems maximize space utilization by storing multiple pallets or cartons in deep lanes, significantly increasing your storage capacity.
- Efficient Inventory Rotation: The FIFO design ensures that older stock is always used first, making these systems ideal for managing perishable items or products with expiration dates.
- Enhanced Productivity: Gravity-driven flow systems reduce the need for manual handling and decrease travel time for pickers, speeding up order fulfillment processes.
- Reduced Labor Costs: Automated inventory movement within the rack minimizes the need for forklifts or manual intervention, leading to lower operational costs.
- Versatility: Suitable for a wide range of products, from heavy pallets to smaller cartons, these systems can be customized to meet the specific needs of your warehouse.
Is Pallet Flow / Carton Flow Racking Right for You?
Pallet flow and carton flow racking are ideal for industries with high turnover rates, such as food and beverage, pharmaceuticals, and e-commerce, where speed and inventory accuracy are critical. If your operation requires efficient stock rotation and streamlined picking processes, these systems offer a reliable solution.
For more information on how pallet flow and carton flow racking can transform your warehouse’s efficiency, contact us today to develop a solution that matches your operational needs.
Pick Modules: Streamlined Order Fulfillment for High-Speed Operations
Pick modules are multi-level racking systems designed to optimize order fulfillment in high-volume distribution centers. These systems integrate various storage types—such as pallet racks, carton flow racks, and conveyors—to create a seamless flow of products, allowing for faster and more efficient picking, packing, and shipping processes. Pick modules are ideal for businesses looking to increase throughput and maximize space utilization.
Key Benefits of Pick Modules:
- Enhanced Order Picking Efficiency: By consolidating storage and fulfillment into one streamlined system, pick modules significantly reduce pick times, making order processing faster and more accurate.
- Increased Storage Density: Pick modules can be customized to include multiple levels, maximizing vertical space and improving overall storage capacity without expanding your warehouse footprint.
- Versatile Design: These systems can be tailored to your specific needs, incorporating various storage types and automation elements to accommodate a wide range of product sizes and shapes.
- Scalability: Pick modules are easily adaptable, allowing you to expand or reconfigure the setup as your business grows or as your order fulfillment needs change.
- Reduced Labor Costs: The integration of conveyors and other automation technologies minimizes manual handling, leading to lower labor costs and increased operational efficiency.
Is a Pick Module Right for Your Operation?
Pick modules are particularly beneficial for operations that handle a high volume of orders with diverse product lines, such as e-commerce, retail, and consumer goods industries. They are ideal for businesses aiming to boost order accuracy and speed while reducing costs associated with labor and floor space.
For more information on how pick modules can transform your order fulfillment process, contact us today to design a solution that fits your unique needs.
THE RESULTS
Did you know?
Benefits of Pallet Racking
Pallet racking systems offer numerous advantages in the warehouse industry:
- Space Optimization: Make the most out of your warehouse space.
- Efficiency: Speed up loading and unloading processes.
- Safety: Properly designed systems can significantly reduce workplace accidents.
SAFETY
Safety Guidelines
Safety is paramount when dealing with pallet racking in the warehouse industry. Always adhere to the following guidelines:
- Regular inspections
- Proper training
- Load limitations
PRACTICES
Best Practices
To get the most out of your pallet racking system, consider these best practices:
- Choose the right type of racking for your specific needs.
- Regularly audit and adjust your system for optimal performance.
- Invest in quality over quantity.
DECISION
Conclusion
Pallet racking systems are an essential component in modern warehouse operations. From enhancing space utilization to improving safety and efficiency, the benefits are numerous. Choose the right system for your warehouse and adhere to safety guidelines to get the most out of your investment.